Though the bag business is finally catching on to the need to use recycled materials and other textiles that already exist, few companies actually make products as nice to look at as they are functional.
Enter Portland, Oregon’s Truce Designs, a one-man business making bomber backpacks and duffel bags crafted almost exclusively with upcycled sailcloth and other repurposed, high-performance materials like Dyneema and drysuit fabric.
Helmed by jack-of-all-trades Luke Mathers, who has been crafting bags out of recycled sailcloth for the better part of the past decade in a series of workshops and maker spaces around the city, the small brand champions sustainable design practices and American manufacturing.
Though now a well known brand in the Pacific Northwest, Truce has humble roots, as most maker stories do. Mathers was first introduced to the craft as part of Portland State University’s sailing team while learning to sew at the North Sails loft in Portland (under the guidance of the team's coach who owned the space). He began transforming scrap cuts into messenger bags for him and his friends.
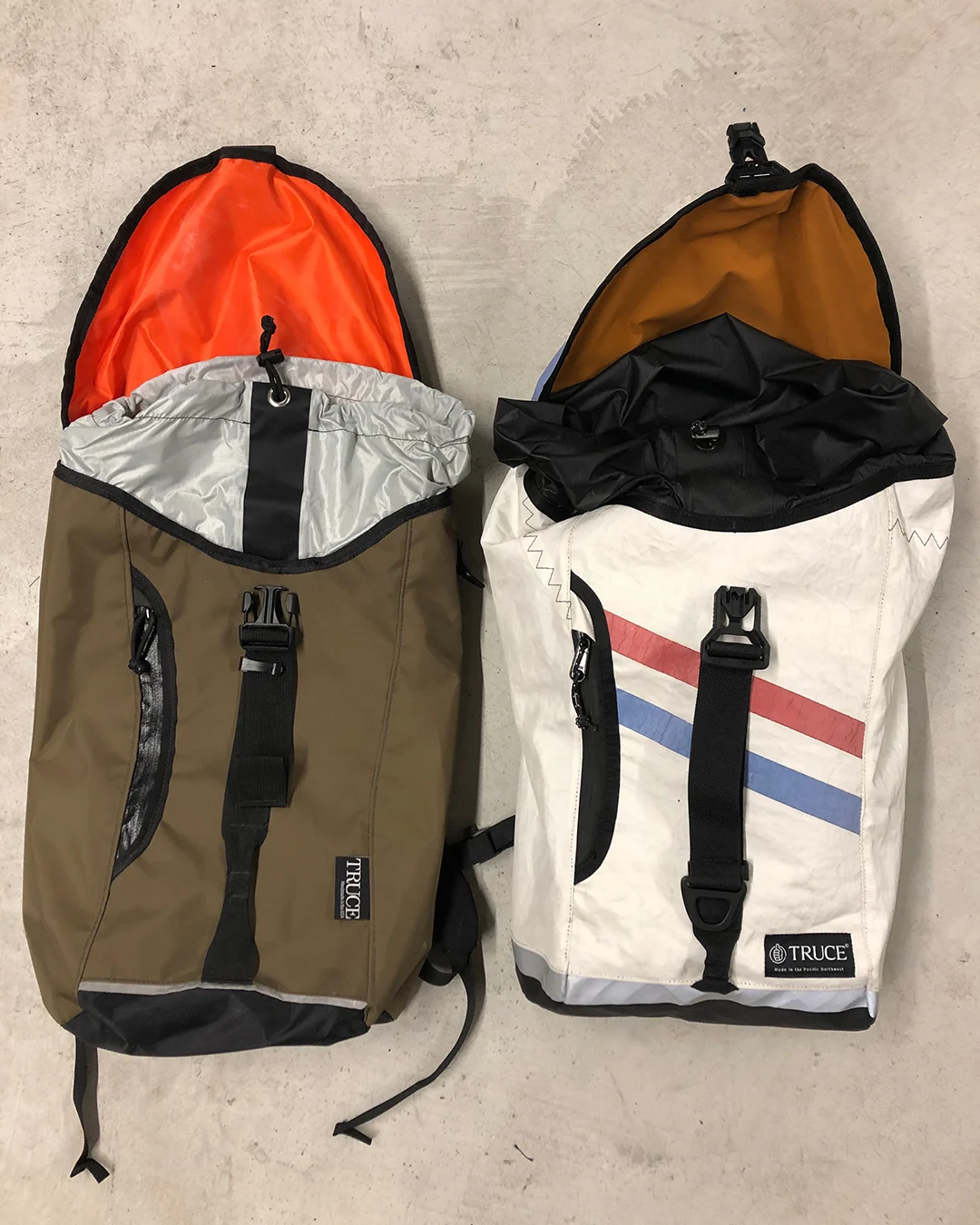
Truce's first ever Drop Liner pack next to a modern iteration
From there he began working with scrap drysuit offcuts too, originally sourced from a local factory, and later, from a major California-based manufacturer of paddle sports gear and apparel. The material turned out to work well for bags, and the environment. (Because drysuits aim to have as few seams as possible, and are sealed using a hot air machine, there ends up being a lot of scrap material left over.)
“Basically, I was saving them a little bit of money on their trash bill and keeping this heavily PU-coated Nylon from getting incinerated or dumped in a landfill,” Mathers explains.
Much of the sourced material winds up in Truce’s flagship Drop Liner backpack, making it weatherproof and ready for adventure, in the city and out. It comes in your choice of four cloth designs and is made of a material that’s probably going to stand up to whatever you’re going to put it through (keep in mind high-grade sailcloth is meant to spend serious time on the high seas).
The benefit of upcycling materials extends beyond simply saving waste—it’s actually easier to work with, too. Mathers explains that working with new sailcloth can be tricky. The material is typically quite crinkly and stiff, which is great for sailing as it makes the boats go faster, but is tough to work with on a personal sewing machine, and can lead to ripping when trying to form the skeleton of a bag. While sailcloth needs years of UV and weather exposure to get pliable enough to work with, drysuit material is flexible enough to use immediately.
A prime example would be a Carbon/Dyneema/Kevlar sail that was used by Team USA Oracle in San Francisco in 2014, which Truce turned into several bags. The material had seen enough wear that he could shape it into a usable design. It also happens to look great, too.
For smaller bags, he uses dinghy sails, which have more flexibility than a synthetic sail.