As an keen reader of Field Mag will note, we're a bit obsessed with A-Frame houses. And how to build them. In 2019 we met Andrew Szeto and his now famous micro cabin in Ontario, Canada. The following year British furniture maker Heather Scott shared her experience creating an absolute peach of a DIY equilateral A-Frame house. Each project brought its own unique moments of learning and triumph.
The latest A-Frame build to catch our eye comes from much closer to home, in the Catskill Mountains just a couple hours north of FM HQ in New York City. It also comes with a new set of experiences, and not all of them pleasant.
Because it's important to show not only the incredible DIY success stories, but also the not-so-smooth cabin builds that likely represent a higher percentage of projects than anyone would like to admit, this story is one we've been looking forward to sharing.
The Hubert A-Frame Instagram account offers an incredible glimpse at the step-by-step A-Frame house build process, but we wanted to get the full experience broken down in one place—from the wrath of carpenter ants and the difficulties of working with small town contractors to the building in a pandemic and pivoting designs to meet a changing lifestyle. Below is just that—everything you need to know about building an tiny A-Frame during a pandemic. Read on and wise up.
(Spoiler: the end result is really awesome, even if the road to completion was a bit bumpy.)
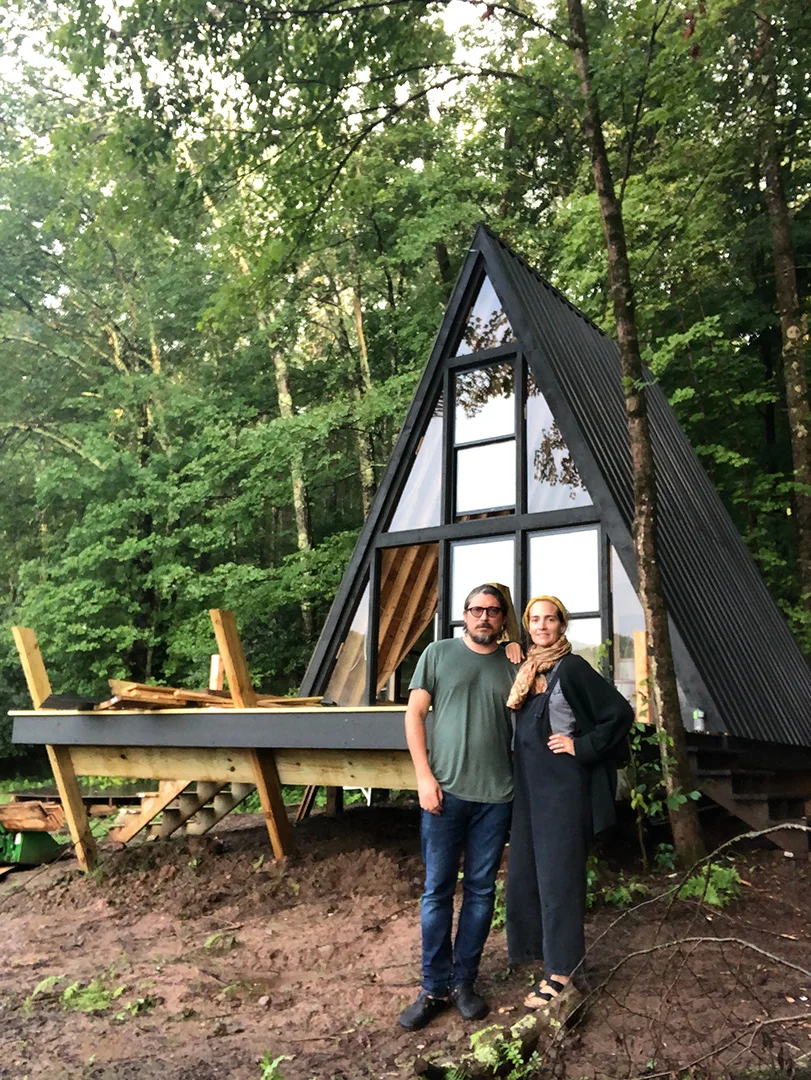
Owners Aaron Griesdorn & Esther Gauthier in Sept 2019
Please introduce yourselves and your project.
Aaron Griesdorn and Esther Gauthier, living between NYC, Paris, and Roscoe in Upstate New York. Having spent the past decades in the city grinding away on building and running our businesses, we would often dream of escaping upstate to enjoy more nature.
We searched for a house for about 4 years and finally landed in Jeffersonville in Sullivan County. We have always been drawn to good design and been intrigued with transforming spaces and businesses, imagining how we would change or renovate something to work better.
You had another lakeside cabin on the land that you first renovated, then tore down, before building the A-Frame. What happened? And what inspired the design shift?
Basically, as we started to renovate the original cabin, we realized that carpenter ants had done a lot more damage than we could see at first. That's when I felt like we couldn’t salvage what was there and perhaps it made more sense to start from scratch.
I became obsessed with the idea of building an A-Frame from then on. I was so worried that the build would take too long and the A-Frame trend would fizzle out by the time we finished haha.
There were a few YouTube videos that I loved and would get me excited about finishing the cabin. One was old school legend Dick Proenneke, and this guy is kind of a contemporary legend too. If anything, these two film series just made me realize that I will probably never build my own cabin... but I totally respect what they did and it's really inspiring.